Formation of Ferronickel Particle from Saprolitic Nickel Ore at 900-1250 °C by Coal and Fluxes Addition
Zulfiadi Zulhan, Windu Shalat, Rifqi, Rachmat Mukti Prasojo
Department of Metallurgical Engineering, Faculty of Mining and Petroleum Engineering, Institut Teknologi Bandung
Email: zulfiadi.zulhan@gmail.com
Extended Abstract
Indonesia posses 5.7 billion tons nickel ore reserve. The amount of mined nickel ore is around 30 – 40 million tons per year and it tends to increase due to the installation of new nickel processing plant especially pyrometallurgy technology such as RKEF (rotary kiln – electric furnace) and blast furnace. High electrical energy consumption is the limitation of the installation of RKEF technology. On the other hand, the operation of blast furnace depends on the coke price where its share is around 40-50% of the nickel pig iron production cost. Therefore, other technology shall be proposed in order to reduce the operating cost of smelting plant. In this research, the influence of temperature and fluxes addition of the formation of ferronickel particle were investigated. The temperature interest is between 900 – 1250 °C. The saprolite nickel ore was prepared and mixed with coal as well as fluxes. The chemical composition of nickel ore is shown ini Table 1.

Table 1. Chemical composition of nickel laterite ore.
Nickel ore was mixed with the addition of 10% coal as reductant. Three fluxes were added with the following composition: 10%CaO; 10%CaO and 10% CaF2; 10%CaO, 10% CaF2 and 10% H3BO3. The mixture was formed into cylindrical briquette using press machine. The experiments were conducted in horizontal tube furnace using graphite crucible under argon inert atmosphere for 2 hours. The results are shown in Figure 1-3. At 10%CaO addition, the ferronickel formation was only observed at 1250 °C with the maximum size is 18 m. At lower temperature, the ferronickel was difficult to observed. On the other hand, the addtion of CaO, CaF2 and H3BO3 initiate and promote the formation of ferronickel particle. The size increases as temperature increases. The maximum ferronickel size is 120 m by addition of 10% CaO and 10% CaF2. The addition of 10% CaO, 10% CaF2 and 10% H3BO3 increases the particle size up to 277 m. Based on SEM-EDS analysis, the nickel content in the ferronickel particle is 8.59% and iron 85.65%.
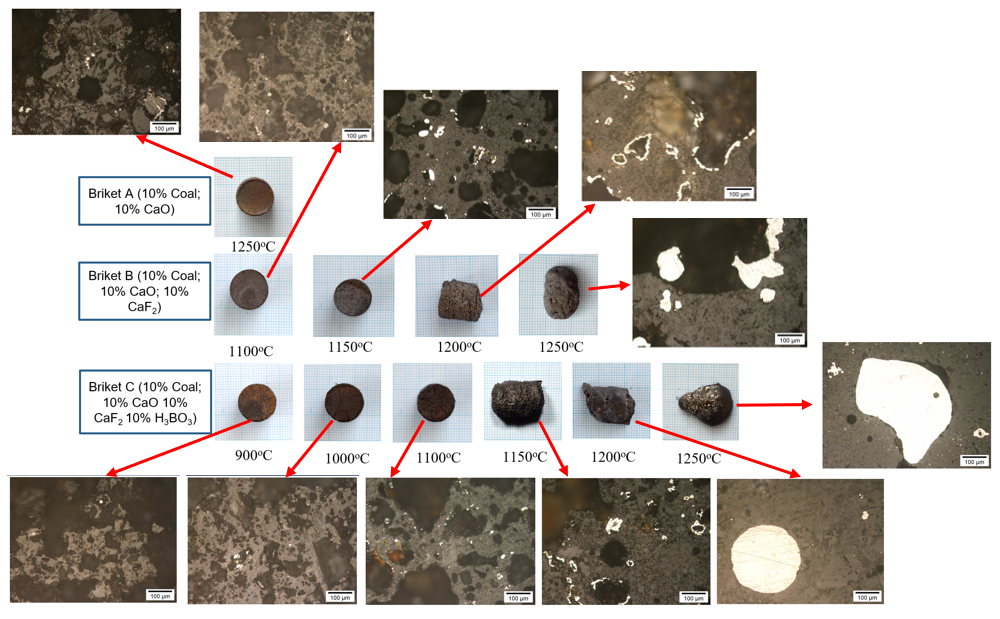
Figure 1. The influence of temperature and fluxes on the physical appearance and ferronickel particle grain size.
Figure 2. SEM-EDS analysis of ferronickel particle.
Figure 3. Maximum ferronickel particle size as function of temperature.